“In the long run, all machines break down” is admittedly a terrible reinterpretation of a famous quote by John Maynard Keynes, the renowned British Economist. However, there is a kernel of truth in it. All machines are prone to wear and tear. In fact, a joint study by Wall Street Journal and Emerson found that unplanned downtime costs industrial manufacturers an estimated $50 Billion per year. Equipment failure is the cause of 42% of this unplanned downtime.
So, what can we do to prevent this colossal loss?
The answer is simple – Employ a more efficient equipment maintenance strategy.
In the early days of the Industrial Revolution, machines were not too complex and that meant fewer breakdowns. As we have entered in to the 2nd and 3rd wave of the Industrial Revolution, with the assembly line and rapid automation through Programmable Logic Controllers (PLCs) respectively, the scenario had changed. There was less of manual labour and more of automation through complex machinery. To remain competitive, factories started measuring and closely tracking various performance metrics including production output, overall equipment effectiveness, personnel productivity etc. Maintenance, which was seen as an activity to be undertaken only when there was a breakdown, became much more important. The strategy of regularly scheduled, preventive maintenance became popular. This periodic inspection of the machinery helped identifying issues early so that breakdowns could be minimised and production stoppages reduced.
As we enter the 4th wave of the Industrial Revolution also known as Industrial Internet of Things (IIoT) or Industry 4.0, there is a greater focus on equipment utilisation, operational cost, worker productivity etc. Industrial IoT is all about connecting low-cost sensors to gather machine data and using advanced analytics to draw meaningful insights. It is estimated that Industrial IoT will allow manufacturers to increase their productivity by 30% The maintenance strategy that employs advanced analytics to predict machine failures is known as Predictive Maintenance.
In a survey carried out by the World Economic Forum (WEF), the most widely cited application of the Industrial IoT is predictive maintenance and rightly so. Predictive maintenance allows manufacturers to lower maintenance costs, extend equipment life, reduce downtime and improve production quality by addressing problems before they cause equipment failures. However, to realise these benefits, a robust digital infrastructure must be put in place and that includes the deployment of an IoT platform like the Microsoft Azure IoT Suite and the use of statistical techniques such as machine learning and predictive modelling to analyse machine data.
Predictive analytics helps us to predict future outcomes using past data. However, it is important to understand that predictive analytics is a journey and not a destination. It starts with identifying the right set of data points, integrating with the machine to ingest real-time data and improving the data quality through live tracking of machine failures. Data preparation and data quality are the key inputs for any predictive model. More high-quality data we can feed into the predictive model the better its accuracy.
All this may seem a little daunting since analytics is not a core function within a manufacturing setup, but there is help out there from companies like Microsoft that provide IoT technology solutions and Happiest Minds that provide IoT engineering services. Together, we can help manufacturers to focus on their core operations and not worry too much about things like asset utilisation and equipment uptime.
For more on Predictive Maintenance, do attend the webinar titled “IoT in Action: Predictive Maintenance” organised jointly by Microsoft and Happiest Minds on 11th Jan 2018. Register for the webinar
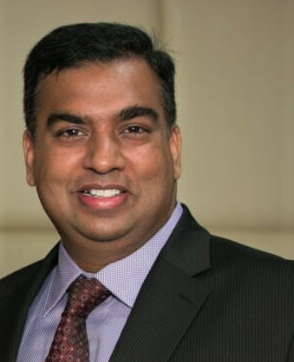
Sudhama is a former Happiest Mind and this content was created and published during his tenure.