The technology landscape has been shifting rapidly in the last few years and the use of varied control systems such as robots and computers is changing the way traditional industries operate. As Industrial Automation begins to take center stage, end users and industrial automation suppliers are faced with an important quandary. They must weigh the risk of adopting new technologies that may result in heartburns against the possibility of losing market share to compatriots who are willing to experiment to stay ahead of the curve.
As a result, quality assurance methods, need to constantly evolve and keep pace with the demands of modern-day industrial automation systems. However, testing programs are often an afterthought in most industrial entities or business enterprises and most existing approaches use physical devices such as gateways, communication modules and sensors for validation.
To address this important gap in the testing process, I recommend a hybrid testing approach that covers both manual and automated testing. As manual testing is fairly well established today, we are going to largely focus on test automation along with simulated testing.
Traditional Industrial Testing approaches majorly involve the use of physical devices such as cloud platforms, gateways, communication modules and sensors covering three test levels namely system testing, site acceptance and factory acceptance testing. Â The shortcoming in this approach is that component validation of the firmware happens very late into the system test cycle. It also leads to higher costs due to multiple test setups while adding greater lead time during regression cycles.
REQUIREMENTS OF A HYBRID TEST APPROACH
A robust test automation framework is the first and foremost requirement of a hybrid test approach. Some important considerations of the framework include:
- Support for the various industrial protocols at various stages of Industrial deployment ecosystem.
- CLI, GUI and API test Automation
- Development of the Software Protocol Data Simulators
- Support for the PID and business logic validations
- Integration with Test Hardware and external vendor tools provided
- Security & Performance Test Automation support
- Extent of need for the Technical and domain knowledge for test case scripting.
- Detailed business driven test execution reports
Test Framework Development
The proposed hybrid test automation needs to have both test automation framework and simulated testing. This needs to be designed in such way to cover the device layer (physical hardware), programming control layer (i.e. PLC, Gateway) and control layer (ie HMI/Scada system) and simulated testing integration. There are different approaches that one can choose from –
TDD (Test Driven Development) – A test first development technique where the test cases are written first to ensure the goal of the development steps and implemented code satisfies the requirement.
BDD (Behavior Driven Development) – An evolution of TDD where the tests are defined based on a user story written in a specific format and based on system behavior.
Data-Driven Testing – Complex interaction sequences can be implemented as repeatable automated test cases wherein test data is separated from implementation.
Key Driven Testing – creating a set of keywords and data tables wherein the functionalities are captured and translated into steps, irrespective of dependence on the automation tool.
The core components of this framework would be configuration utilities, protocol data simulators, opensource libraries, custom built libraries for IA protocols, sensor simulations, key word library, CLI, API, GIU support, libraries for data parsers, cloud connect, and integration with a CI/CD pipeline
PROTOCOL & DEVICE SIMULATION IS EQUALLY IMPORTANT
In the second part of the hybrid testing approach, protocol and device simulation play a key role in accelerating the time to market of the product and solving the after-sales support problem. Sensor simulators with GUI based on PyQt or similar languages can be designed to leverage the Open-source technological support available today.  PyQt provides an easy way to design user interfaces with inbuilt designer tools that provide support integration with the test automation framework. Sensor Simulators will be a dedicated development activity to achieve higher test automation coverage at every stage and to reduce capex of the required hardware. This will also facilitate better facilitation of software development cycles, increasing the test automation coverage significantly along with corner error handling test cases.
As a result, this approach directly results in capex savings by eliminating the need for complete test setups for each developer and test engineer. In addition, it provides extensive coverage, cycle time reduction, reusable test automation scenarios for multiple products and convenient migration or integration into existing test tools.
With the technology evolution that is being driven by Industry 4.0, there are great demands being made on the further development of OT and IT systems. Therefore, new or enhanced product development processes will have to be created and a hybrid testing approach is key to supporting this product transformation by significantly improving quality assurance levels through advanced test automation and bringing about cost optimizations through simulation based testing.
Ultimately, the success or failure of product architectures in the Industrial Automation industry would be determined by their ability to meet the requirements of a thriving and constantly evolving Industry 4.0 ecosystem.
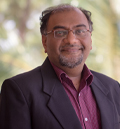
is general manager of Product Engineering Services at Happiest Minds Technologies. He is responsible for defining and leading Test Engineering solutions in the area of Datacenter Technologies specially focused on SDN and NFV technologies. Jason is also responsible for embedded and Systems and device related technologies associated with Internet of Things and Industrial Automation. He has over 24 years of experience in Telecom, Datacom, Networking and IoT product development and testing working across Network Equipment Provider, Telecom Service Provider, Hi-Tech and Manufacturing customers with specialization Networking and Testing, QA. Before, Happiest Minds, Jason has held multiple senior roles in Large PES organizations based in India and did work stints in US and Europe.