Azure IoT revolutionizes gearbox diagnostics and warranty claim validation. Its advanced technology and robust features ensure accurate and efficient processes, saving time and costs.
Why is accurate diagnosis and controlling gearbox malfunctions important?
Gearbox malfunctions and poor diagnosis pose significant challenges for businesses, like costly repairs, disruptions in operations, and dissatisfied customers. The requirement for accurate diagnosis and validation has the following benefits.
-
- Streamline the resolution process, mitigate downtime, and uphold customer trust.
- More efficient resolution process, minimizing the time and resources required for repairs.
- Quicker turnaround times and improved operational continuity.
- Reduction in downtime translates to increased productivity and operational efficiency.
- Swift resolution will increase customer trust.
- Satisfied customers would recommend the business to others.
- Enhances overall operational efficiency.
Implementing IOT-based solutions for better gearbox management and reducing warranty claims Â
Happiest Minds incorporates the following features as part of the approach:
- Remote Monitoring: With remote monitoring capabilities, customers can oversee their gearbox from a distance, minimizing the need for on-site visits and improving response times in case of issues. This empowers customers to identify and address problems before they escalate promptly.
- Asset Management: The solution integrates asset management systems that track gearbox usage and maintenance history. This provides valuable insights into customer gearbox performance over time, allowing customers to identify trends and potential issues, facilitating actions to enhance gearbox performance and minimize downtime.
- Predictive Analytics: Through the collection and analysis of data on gearbox performance, customers can utilize predictive analytics to pinpoint potential issues and proactively address them. This proactive approach aids in reducing downtime and maintenance costs, ultimately improving gearbox performance and customer satisfaction.
- Predictive Maintenance: Customers can employ condition monitoring systems that offer real-time data on gearbox performance, predicting potential issues before they lead to gearbox failure. This proactive strategy enables customers to schedule maintenance activities efficiently, minimizing downtime and reducing maintenance costs.
Addressing the complexities of gearbox malfunctions and warranty claims. This cutting-edge solution harnesses the capabilities of IoT devices, cloud computing, and data analytics to deliver real-time insights and actionable information for precise diagnosis and efficient validation.
- Device Integration: This is like connecting gearbox to a network so it can send and receive data. This is done by attaching special devices (IoT devices) to it.
- Edge Computing (Optional): This is like having a minicomputer on the gearbox that can process data immediately instead of sending it to a far-off data centre or cloud. It’s faster and can be helpful when we need quick responses.
- Data Ingestion: This involves collecting real-time data from gearbox (like rotation speed or temperature).
- Data Processing: After the data is collected, it’s analysed using Analytics which help to find patterns or insights, such as wear and tear on the gearbox.
- Storage: After processing, the data is stored in a database for future reference or further analysis.
- Visualization and Monitoring: Utilize the potential of AI & ML to scrutinize stored data, generating predictive maintenance and analysis reports. Create visual representations, such as charts or graphs, for enhanced comprehension. This enables real-time monitoring of gearbox.
- Rule-based Alerts: Get an alert if something unusual happens (like gearbox overheating or operating outside normal parameters). This is set up using the rules we define.
- Remote Device Management: Remotely control and update gearbox and its devices.
- Security Implementation: Protecting devices and data from hackers. Measures are taken to ensure that everything is secure at the device level and while data is being transferred.
This architecture diagram illustrates the various components of an Azure IoT solution. The devices connect to the IoT Hub, which provides bi-directional communication with the back-end application. Stream Analytics processes real-time data, which is then stored in a SQL Database for further analysis and reporting. Machine Learning algorithms predict potential failures, and Power BI dashboards provide data visualizations for easy understanding and decision-making.
Happiest Minds customers have leveraged below benefits by implementing the above approach:
- Optimization of customers’ equipment working conditions, resulting in a noteworthy 20% reduction in wear and tear
- 35% decrease in repair and warranty claim expenses,
- Substantial extension of equipment lifespans by 70%.
- Significant cost savings, enabling customers to reduce operational costs by 45%.
- Improved equipment and its spare parts pre-shipping procedures, fostering better organization and achieving notable cost efficiencies.
- Access to critical insights into the working conditions of equipment, providing valuable information for informed decision-making.
Conclusion
Accurately diagnosing gearbox malfunctions and validating warranty claims are crucial aspects of gearbox maintenance. With Happiest Minds solution, we can overcome the common challenges faced by end customers like operation overheads, downtime, costs, and smooth operations.
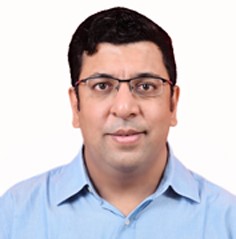
boasts over 20 years of expertise in Microsoft Technology, Cloud Solutions (AWS and Azure), and Enterprise and Integration Solutions. Renowned as an adept professional, he excels in crafting products and modernizing legacy applications using cutting-edge technologies. Kedar’s extensive consultancy experience spans the Manufacturing, Automobile, and Oil and Gas industries.
Currently serving as a valuable Center of Excellence team member, Kedar plays a Sr. Architect role at Happiest Minds. His contributions involve not only providing innovative solutions but also actively participating in building capabilities in new technologies and fostering competency within the team.